The Squeeze on the Mash Filter Press
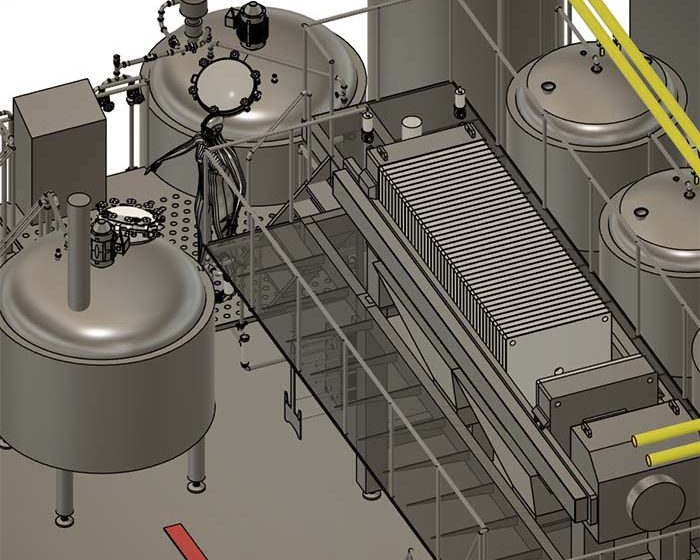
Mash Filters, Mash Presses, Filter Presses – the Basics
When it comes to brewing beer and distilling spirits, most people think of hops, barley, brewing kettles, and copper stills. While this is all well and good, there’s an unsung hero in both industries quietly revolutionizing the process: the filter press. Often called a mash filter or mash filter press, this fascinating piece of equipment is a game-changer for brewers and distillers aiming for increased efficiency, superb quality, and sustainability in the face of rising material costs.
At its core, the mash filter press is a sophisticated device designed to separate liquids from solids using a squeezing action. Traditional lautering methods involve a lot of patience where gravity slowly extracts the liquid from the spent grain bed, but the mash filter press brings a modern twist to this age-old task. Imagine a giant sandwich press, but instead of grilling a panini, it’s squeezing every last drop of precious liquid using inflatable plates. This marvel of engineering not only streamlines the process but also significantly improves yield and clarity, making it a vital tool for modern beverage production.
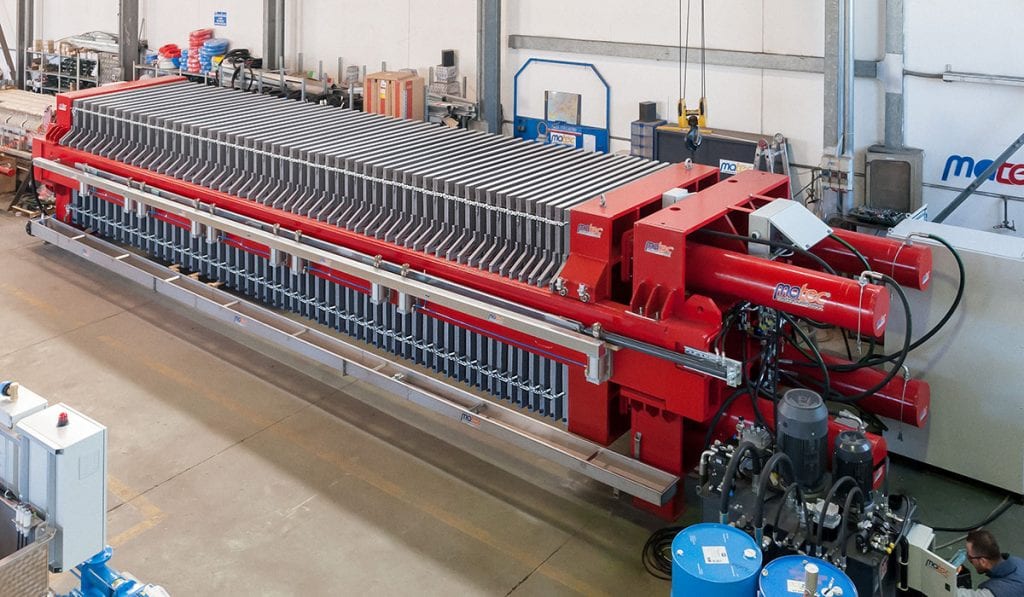
Humble Beginnings
Mash filter presses have their roots in industrial processes where they are known generally as filter presses. From waste water to mining, their ability to effectively separate solids from liquids quickly and efficiently has made them a go-to solution. Over time, innovators saw the potential to adapt this technology for brewing and distilling. While they’ve been part of the brewing industry since the late 19th century, their use has grown significantly in the past few decades as breweries and distilleries seek more efficient and sustainable methods. While still much more uncommon than traditional lautering in breweries, in Scottish distilleries, filter presses are now considered the perfect solution to making scotch wash.
Video of the Author inspecting an automatic plate shifter for a new fully automatic mash filter press prior to shipment
One of the standout benefits of using a mash filter press is its efficiency. Traditional mash tuns can leave behind up to 30% of fermentable sugars, but the filter press reduces this loss to nearly zero and combined with a muti-turn brewing schedule can actually surpass 100% efficiency. For breweries and distilleries, this means more product from the same amount of grain, translating to cost savings and a more sustainable operation. On average a mash filter brewing system will use 10% less grain and 30% less water than traditional 4 vessel lautering brew house.
Mash Filters Turn Efficiency into Sustainability
This increased efficiency is a boon for sustainability. Using less grain and water to produce the same amount of beer or spirits reduces the strain on agricultural resources and water supplies. As the world becomes more conscious of environmental issues, the role of technology in promoting sustainable practices is more critical than ever. The mash filter press is an excellent example of how innovation can help industries reduce their environmental impact while maintaining high-quality standards. By minimizing waste and optimizing resource use, mash filter presses contribute to a more sustainable and responsible approach to beverage production.
On average a mash filter brewing system will use 10% less grain and 30% less water than traditional 4 vessel lautering brew house.
The mash filter press also shines in its versatility. It can handle a wide range of grist compositions, from the finest pilsner malt to the chunkiest adjuncts, and everything needed for various spirits. This flexibility allows brewers and distillers to experiment with different recipes and styles without worrying about stuck mashes or inconsistent extractions. In other words, it’s the best friend of the adventurous artisan looking to push the boundaries of what beer and spirits can be. This adaptability not only enhances creative freedom but also ensures consistent quality across diverse product lines.
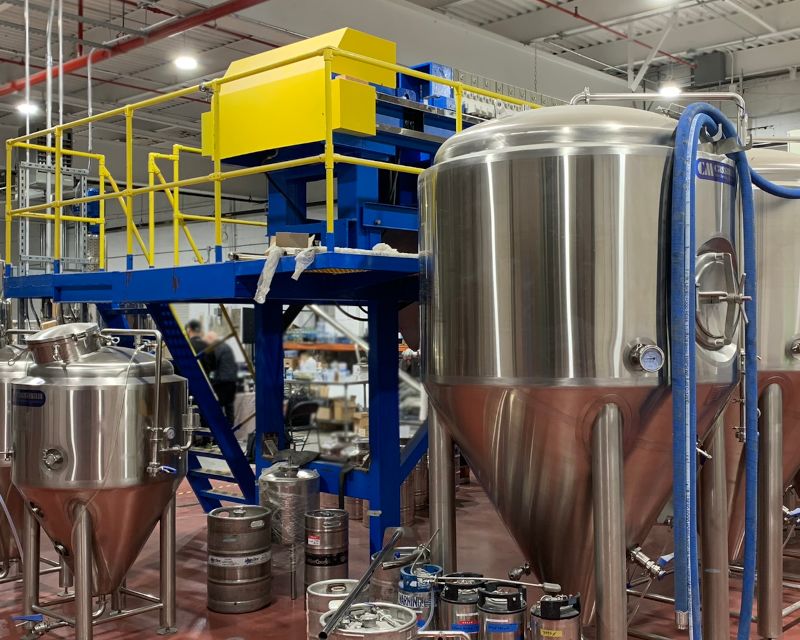
But it’s not all about efficiency and versatility—let’s talk about quality. The mash filter press produces a clearer wort and cleaner fermentable liquids with fewer impurities, leading to a cleaner fermentation and, ultimately, a better-tasting product. It’s like the difference between a rough draft and a polished final copy: both get the job done, but one just shines a little brighter.
Even more interesting is the ability to use a wide variety of difficult or even impossible grist bills. 100% rye or corn, no problem at all and no stuck mash or soggy stillage to worry about. We can also engineer post processing into a filterpress system with the goal of creating a disposal or re-use ready spent grain or stillage, in some cases eliminating centrifuges and dryers.
You might be thinking, “This all sounds great, but what about the cleaning?” While it’s true that filter presses are more complicated than their lauter tun cousins, when properly designed they should all but clean themselves. With automated plate shifting systems and easy-to-clean plates, these systems are designed not only for a high level of cleanability, but for quicker turn times as well. Think of it as the Roomba of the brewing and distilling world: doing the dirty work so you can focus on crafting the perfect brews and spirits.
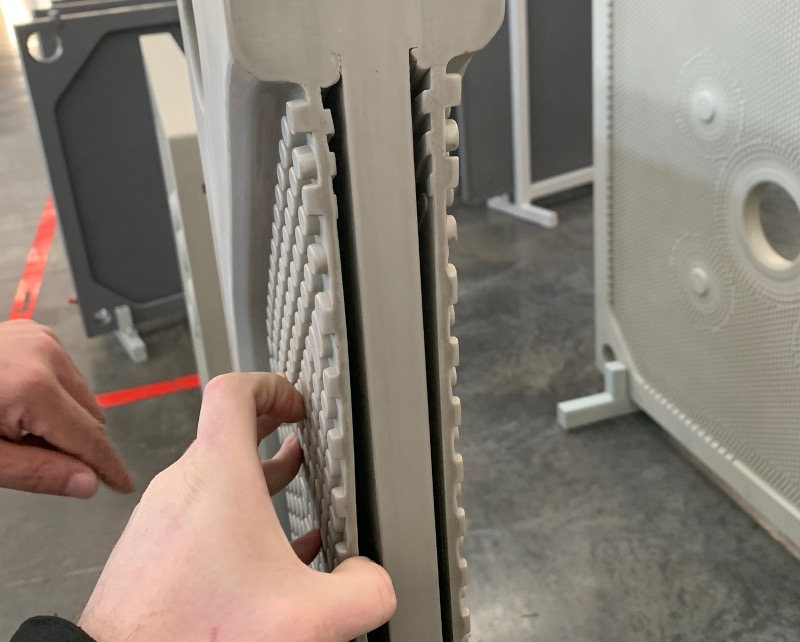
The mash filter press is the perfect tool for brewing and distilling industries, offering significant improvements in efficiency, quality, and sustainability. For brewers and distillers looking to enhance their operations, The Engine Room is ready to help you make the leap and join the future of beverage production. Contact us today to explore how we can assist you in optimizing your production processes.