Don’t Let Stillage Be a Whale of a Problem
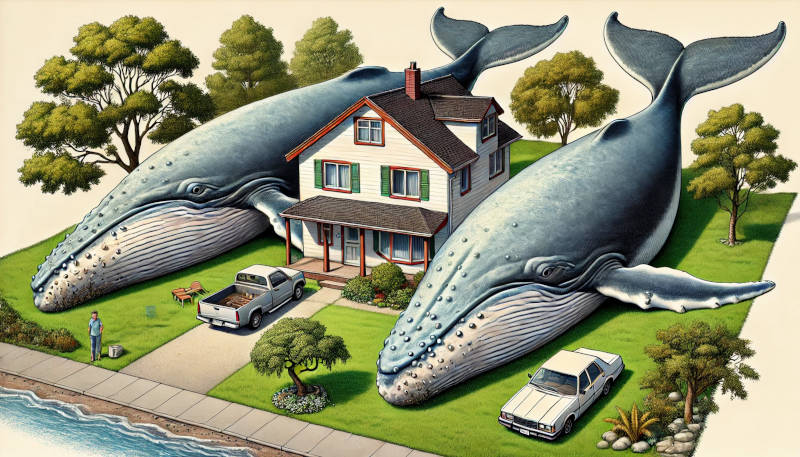
Originally penned by Engine Room distiller and engineer, David Kyrejko, an edited version of this piece was written for Matrix Technologies Inc. You can read the published version of this article and more at Distillery Trail Magazine
This isn’t a 101 on stillage – it’s more of the warning that hopefully is printed in bright red, 100pt type on the very first page before you even start that read. I’m not going to drill you on how centrifuges spin and dryers dry, we’ve got bigger issues to deal with and we’re going to get right into it.
So, let’s set the stage: two years ago you went for it. You took the plunge and made the moves to open that distillery you’ve been meticulously planning. You spent months going over all of the details and everything had to be perfect, with an unflinching eye towards all things quality.
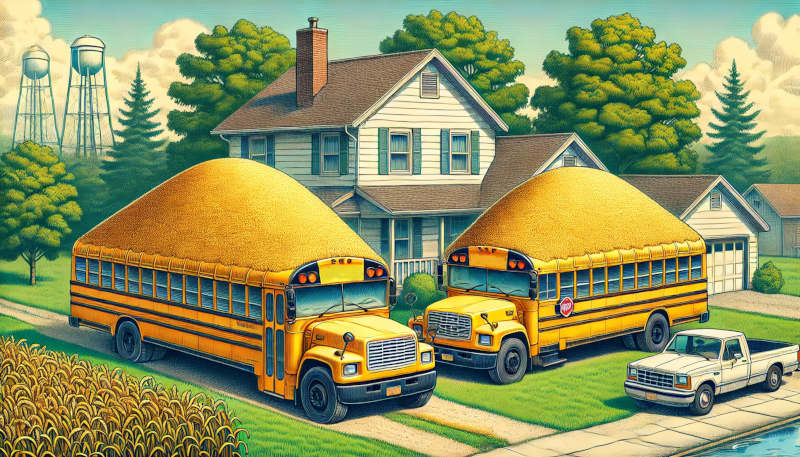
Everything’s coming together nicely. That custom built combination column and pot still to forge your world-class all-grain spirits, you’ve commissioned a tasting room any designer would drool over, the award-worthy labels are exceeding your expectations, secured contracts for sustainably grown grains from local farmers, and developed a marketing plan that even your most skeptical investor feels is air-tight. No expense has been spared on the launch and your first batch is your pride and joy.
Once the excitement wears off, the details catch up with you and it truly stinks. Seemingly overnight, a shocking amount of soggy stillage has started to accumulate and worse, it seems to be growing instead of shrinking. The farmers you were told would take your unprocessed stillage haven’t really been beating down your doors to get at the goo, but since you’re in start-up mode, you’ve chalked it up to growing pains. A week goes by and those pains reach absolute agony as you hand over a check to a hazardous waste disposal company to deal with your backlog of putrid, moldy stillage.
You’ve run into the iceberg to the modern distillery’s Titanic – the hidden danger of not engineering a stillage processing and disposal solution.
Or maybe you went the municipal waste disposal route. The parade of trucks seems endless and you’re beginning to come to terms with the high cost of simply hauling raw stillage. Even with the slop dewatered, the weight is enormous! When you look at the numbers it’s almost like you’re using diesel fuel to make the stillage disappear – there goes your sustainability mission statement.
Let’s not forget the NIMBY (Not In My Back Yard) factor… it turns out your industrious small business neighbors absolutely love having your beautiful new distillery around – as long as they don’t have to smell you. The plan was to try to discreetly store the stuff on-site, but you hadn’t planned on the sheer size of that project. Any setback immediately puts you behind and you can’t seem to get back on track. The neighbors have soured on you, much like the aroma wafting off your disposal site.
With a screech, your humming distillery grinds to a smelly, sticky, hazardous, utterly expensive and confusing halt. You’re not alone though, every year distilleries of all sizes are brought to a stand still by this overlooked and absolutely critical (but less exciting) aspect of the business. To say it plainly – not properly engineering systems for handling your waste will shut down your distillery. Period.
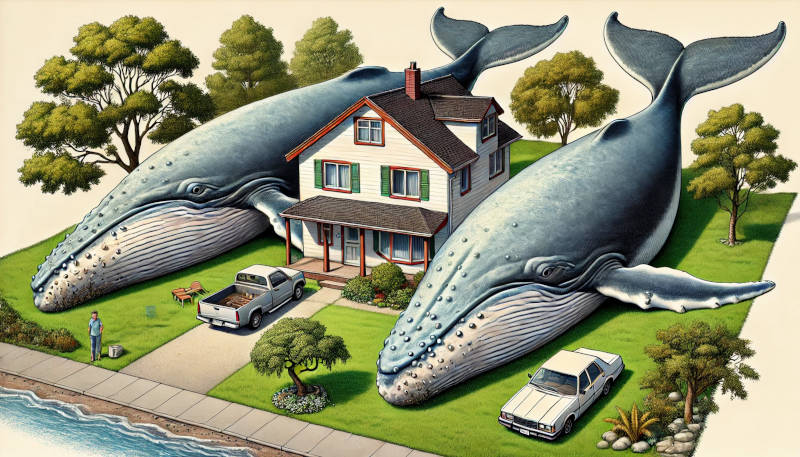
To say it plainly – not properly engineering systems for handling your waste will shut down your distillery. Period.
The reality of the amount of waste that even a modest distillery will put out on a yearly basis can be staggering. “We honestly didn’t realize just how much of the stuff was going to be generated” is a common utterance when a client is finally confronted with the problem. This in itself is one of the root issues, so let’s break it down by the numbers.
A distillery, utilizing best practices, producing 10,000 barrels of finished whisky yearly will generate roughly 130,000 pounds per day of waste stillage. That can be a little hard to picture so let’s put it another way – how about a pair of humpback whales? Ok, maybe a little too exotic – how about school buses? Filled to the brim, the raw stillage produced every day would fill 2 school buses and have enough left over for a Honda Civic or two.
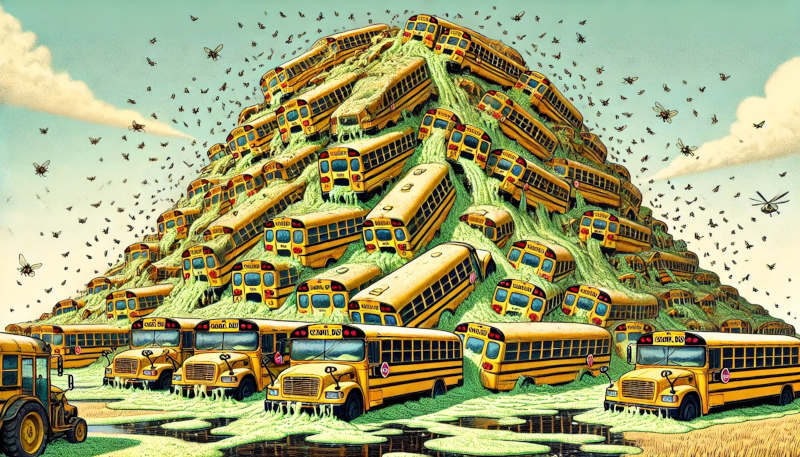
Multiply this daily output by a year’s worth of production and you’re looking at 42 million pounds of stillage, 5 million gallons of goo or going back to our visuals – several generational pods of humpbacks or an entire state’s worth of school buses. It all has to go somewhere and depending on your location this may simply not be readily possible.
This is where things can go downhill fast. Due to its high moisture content and residual nutrients, even de-watered stillage is extremely bio-active and nothing likes this situation more than mold. In only a few short days, mold can take hold and make the situation go from bad to worse.
At this point simple hauling is no longer an option and a hazardous waste disposal contractor will need to be contracted. In extreme cases the toxic stew will have to be incinerated along with your wallet. All the while, you can’t make more product because you physically have no where to put it. No more production means no more money to pay for any kind of remediation taking the situation from worse to absolute worst.
To say it plainly – not properly engineering systems for handling your waste will shut down your distillery. Period.
But hold on, you knew that you had to get rid of waste, this isn’t exactly breaking news. You read about the centrifuges and separators – WDS, DDGS… you know the lingo. You even pulled the trigger on a bunch of equipment to take care of this. Why then is there a whole fleet of stillage filled school buses stinking up your distillery? It’s not enough to just have equipment, it needs to actually be made to do its job and that comes from understanding your needs in the first place.
Seasoned distilleries run like a clock because they know that all aspects of production are intrinsically linked. Shut downs are unacceptable and they have made sure to engineer how stillage, and waste in general, is dealt with from day one. With the larger distilleries hunting down the even sub-single digit percentage losses, how waste is dealt with is a primary concern. If you think dealing in humpback whales and school buses is challenging, these larger distilleries are dealing in freight trains… After-all, what good is trying to squeeze another 1% out of your still if being shut down for a day eclipses that 10 fold?
Tackling Stillage
Not all heroes wear capes, but in this case they do know a thing or two about engineering. An experienced process and distillation engineering group is vital to help a distillery plan from the very beginning how to meet their goals – often even before you go to investors or apply for bank loans. By taking a wholistic approach to all aspects of your production process and utilizing real world experience across multiple disciplines, process engineers are able to formulate systems with resilience to unforeseen hiccups that are one of the hallmarks of the distilling industry.
Did your centrifuge go down? No problem, we designed capacity into the system to keep you in production while it’s being resurrected. Maybe the municipality decided to increase its waste water quality guidelines. That’s Ok, we caught it in the pre-engineering phase and made sure that we provided options that can be plugged in as needed. The farmer down the road closed up shop and no one is taking minimally processed stillage? Nothing to worry about, we clocked that during our discussions and made sure to design your separation system output around an easily transportable stillage standard.
Not all heroes wear capes, but in this case they do know a thing or two about engineering.
By looking at the whole problem rather than just a list of equipment to purchase, a properly engineered stillage solution makes sure you can continue to grow your distillery without worrying about pods of whales and fleets of buses stinking up your neighbor’s backyard.